Homes of the Future?
A First: A Fully 3D-Printed House Made from Bio-Based, Low-Carbon Materials
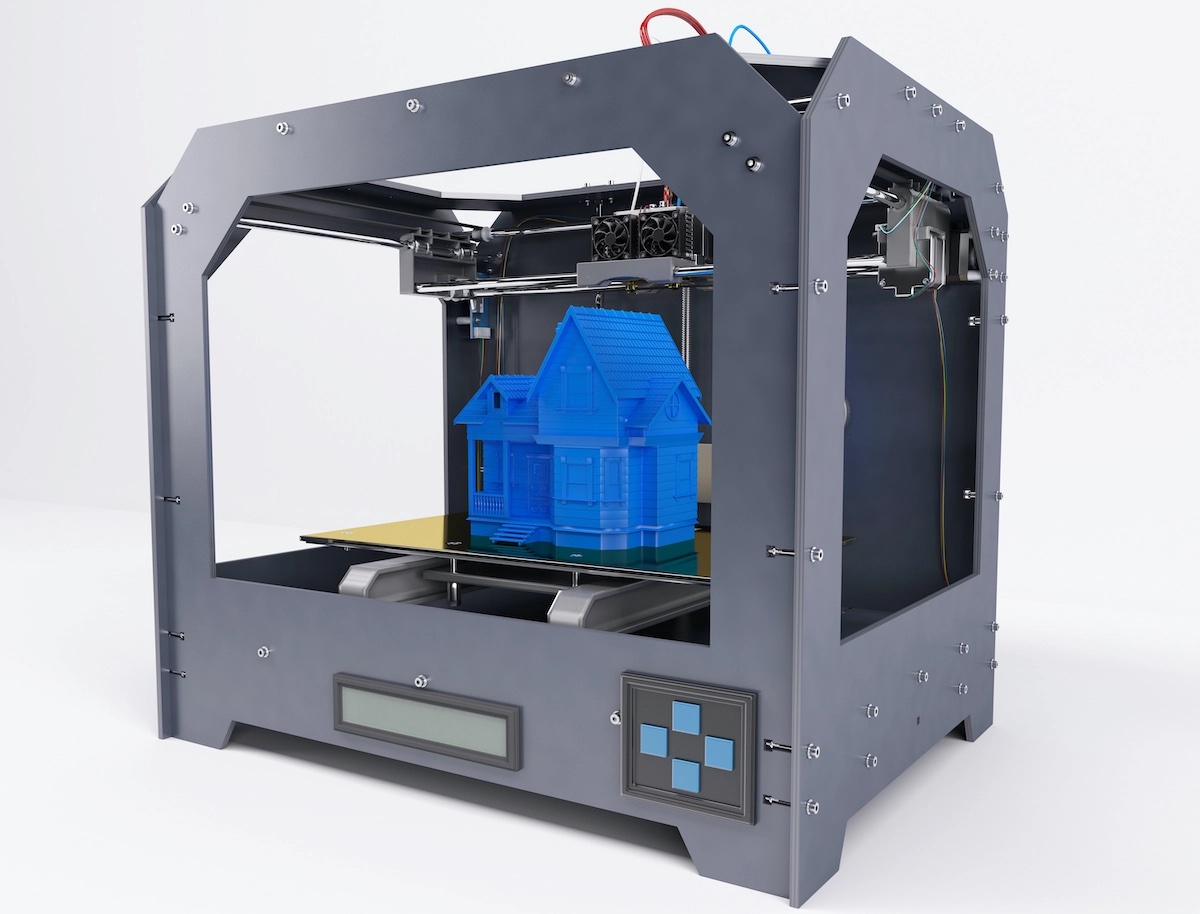
One of my recent articles focused on the big potential of 3D-printed houses. However, the printing process used up until now has only created walls. Carpenters are still needed to install doors and windows, and build the roof. On the plus side, just printing wall panels produces walls of greater tensile and flexural strength and in half the time of traditional practices.
Modular building, panelized construction, and building with structural insulated panels (SIPs) have received attention as new technologies with potential to speed up production and reduce waste. Widely used in some countries, these innovations have been slow to be incorporated in the U.S. While 3D printing could just be another one of these new approaches, it could actually help solve the construction industry’s labor and supply-chain issues.
One building company, Mighty Buildings, has produced the first 3D-printed net-zero home using printed components. The one sustainable drawback of its process, as well as that of all other 3D efforts, is that they use concrete for their walls. The production of cement, the binder in concrete, accounts for around 8 percent of all greenhouse-gas emissions worldwide. In addition to high embodied carbon, concrete has poor insulative properties. Fortunately, new concrete mixes are being fed into the 3D-printing nozzles that are showing promise of reducing emissions by half or more.
The latest campaign in green building is to utilize materials that have low embodied carbon while avoiding materials such as spray and rigid foam, steel, and concrete — all currently being used in 3D-printed houses. However, 3D printing may be on the cusp of conquering this challenge: The University of Maine has produced a prototype printed house made entirely of bio-based, low-carbon materials. The materials exuded by its printer are composites of wood fibers and bio-resins. About 60 percent of the material is wood flour by weight and the rest is resin. According to the team, this building is fully recyclable.
Another breakthrough with the BioHome3D is that all components — floors, walls, and roof — are printed and with high R-values (insulation values). Culminating decades of research by the university team, the printed material resists decay and rot because of the resin that prevents water intrusion. When it is time to recycle, the building can be ground up and sent through a printer to produce another house. Wall and roof sections are printed with an inner and outer layer connected by a truss-like reinforcement. The cavity between the two layers is filled with cellulose insulation. This design allows for increasing the wall thickness and improving the insulative performance as needed.
Construction is a traditional industry, slow to change. It is, however, moving toward net-zero performance buildings. Maybe it will also start making houses that are carbon storage units.
Support the Santa Barbara Independent through a long-term or a single contribution.