The Future of Homebuilding May Soon Be Here
3D-Printed House in the Works for the Housing Trust Fund of Santa Barbara County
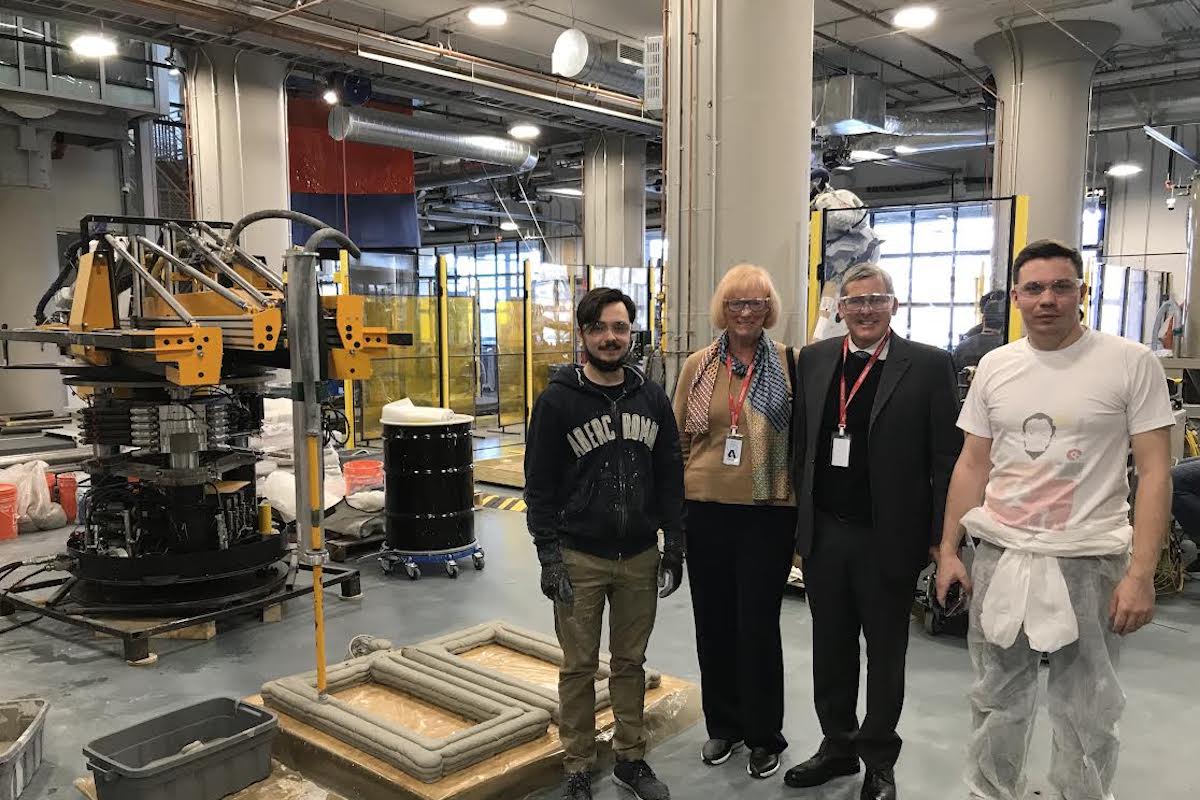
After 46 years developing affordable housing, Jennifer McGovern is ready to take the plunge into 3D-printing a three-bedroom, two-bath home, made by the same company that was a finalist in NASA’s Mars Habitat Challenge.
McGovern leads the Housing Trust Fund of Santa Barbara County, which in the past 20 years has helped build 373 affordable homes through $9.1 million in financing and also put 84 people in Santa Barbara County’s workforce into a new home — both through its loan programs. “We’d been watching the costs go up and up,” she said, “so we began looking at ways to create a paradigm shift, to address the cost issue and make things more affordable.” Since 2018, McGovern and a team of like-minded individuals have been looking into 3D-printed homes, going to visit and talk with Apis Cor, a company now in Melbourne, Florida, that started out in Berkeley before moving to Boston, where it competed in the NASA contest.

To build its structures, Apis Cor developed a machine it named “Frank,” which is mobile and compact, equipped with an arm that extrudes and positions the concrete mixed by a pump called “Gary” and housed in a tanker truck the company named “Mary.” Frank can be set anywhere to build various parts of a structure and can reach up to three stories, according to Apis Cor.
Among the advantages of an extruded concrete house, or a home “3D-printed” through the technology controlling the extrusion, are not only costs but also time. A structure called the “Fibonacci House” was approved in Canada last year, extruded in several large pieces and designed using the blossoming curves of the mathematical sequence. The 377-square-foot structure was completed in only 11 days by Twente Additive Manufacturing. While the permits and planning process for anything in Santa Barbara County could take a year or more, the printing process itself is relatively quick. McGovern is confident and curious to see how this project pencils out.
“This is a prototype, a proof-of-concept project,” she said, “and also a lesson in working with local architects and the local approval process.” The Housing Trust is in the first of three phases for the project, which is to plan all the elements from design engineering to community participation. Next will be construction, and last is the Documentation and Dissemination of Project Findings. Documenting the project is key to doing it again, McGovern said, and the report will collect information on the 3D process, how it works, and how much it costs. For comparison purposes, they already know that building a home like this costs about $905,000 currently, and a two-bedroom apartment costs about $550,000, both more than low- and moderate-income residents can afford.
The land for the project belongs to the Cambridge Drive Community Church, which was intrigued by the thought of building a unique and affordable home on its land, which is zoned for a single-family residence. The 3D-printing process, which is not yet in the California Uniform Building Code, will only create the walls of the home; the foundation and roof will be built using conventional means. Working with the City of Goleta’s planning department, McGovern’s team was told it might be possible if the engineering calculations work out with the building code.

Safety was also a consideration for the Fibonacci House, with freeze-thaw performance, thermal conductivity, and thermal expansion among the necessary criteria in British Columbia. Another 3D-printed home going through its paces in Los Angeles by Contour Crafting Corporation achieved acceptance for structural performance and fire resistance from the International Code Commission last summer.
SBCAG, the Santa Barbara County Association of Governments, chose the Housing Trust’s 3D-printed house for a $375,000 grant from the state’s Regional Early Action Planning fund in December. Montecito Bank & Trust also gave $100,000 from the Michael Towbes Community Impact Grant for the project, and the Housing Trust itself has committed $300,000 to develop the idea.
“Nothing’s guaranteed until the state approves the project,” McGovern cautioned, adding that the trust also must fundraise a few hundred thousand dollars more to really complete the project and its goal of compiling a report. But if it proceeds, community meetings will take place for the project, as well as an opportunity to view Frank in action.
McGovern said Apis Cor has built a home in as few as four to five days before. If all goes well, about this time next year, a very unique, affordable house may stand on Cambridge Drive.
Support the Santa Barbara Independent through a long-term or a single contribution.
You must be logged in to post a comment.