Time for the Cement Industry to Clean Up
Tradition and Cost are Hurdles to Transforming a Big Polluter, but Not Insurmountable
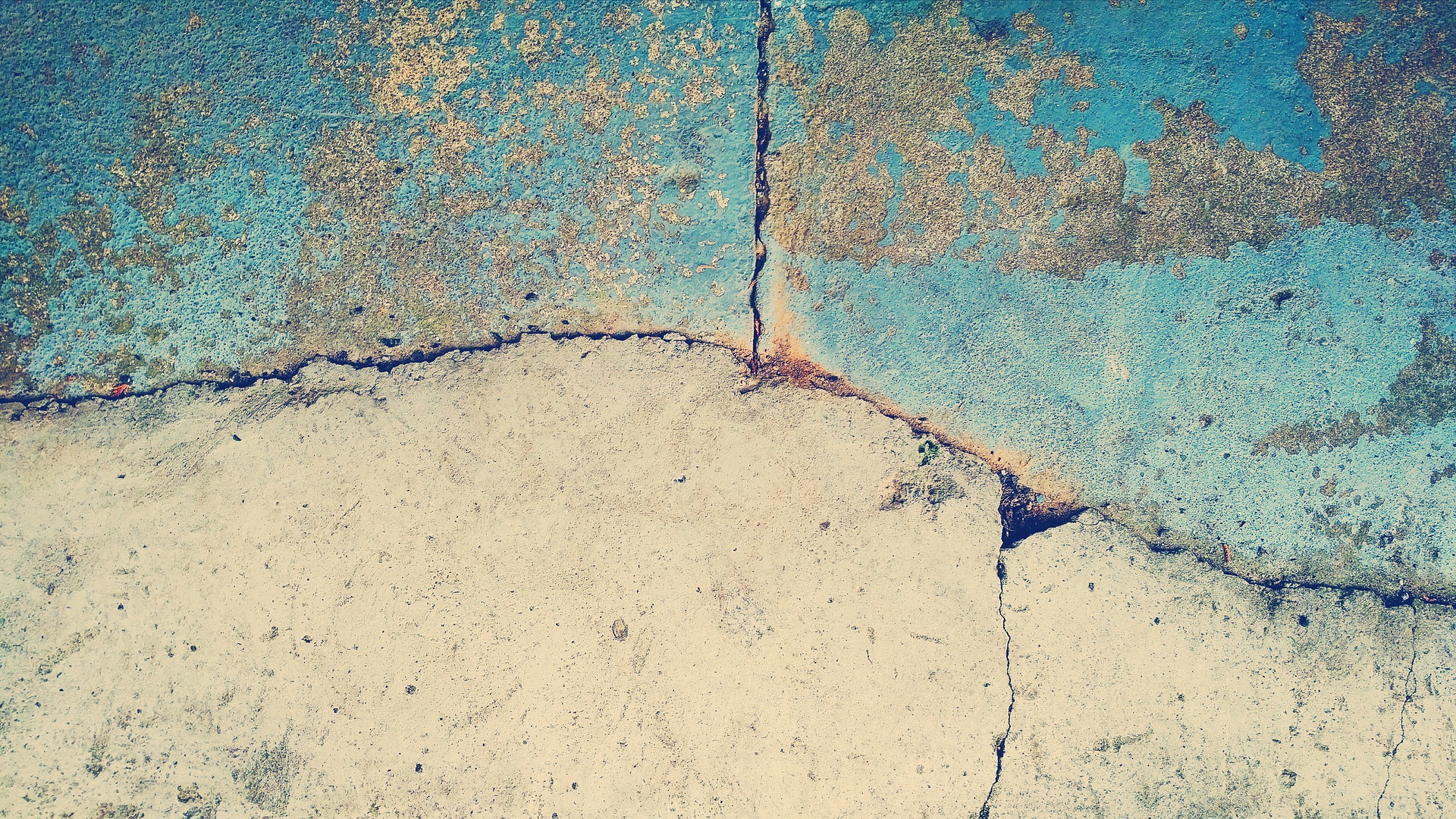
The cement industry is one of the most polluting and carbon intense of all industries, producing three times the carbon emissions of the aviation industry. Its products are ubiquitous: the basis of foundations, roads, dams, and airport runways. Every phase of concrete spews massive amounts of CO2 into the atmosphere. The worst phase, however, is the manufacturing one, where half of the pollution comes from the energy to heat limestone to 1,500 degrees Celsius and the other half from the chemical process of breaking down the limestone into calcium oxide. To get the high temperatures required, coal is the preferred fuel.
One of the most straightforward ways to reduce emissions is to transition to cleaner-burning fuels. Some plants are using old tires, a great source of energy and one of the most effective ways of disposing of used tires. Even cleaner options are starting to be tried, namely, hydrogen-based fuels and electricity generated from wind and solar.
As suggested above, energy for high heat is only part of the concern. The other is the CO2 released during limestone’s chemical transformation into “clinkers,” chunks subsequently ground into powder to become Portland cement. For many years, the construction sector has been making substitutions for Portland cement in concrete mixes — the most prevalent being waste products like fly ash or rice husks. Consequently, industry-wide, the amount of clinkers has been reduced by about 30 percent since 1990.
Cement/concrete is cured by adding water. Several innovative companies are creating cements that need to absorb CO2 in order to harden. For every ton of this cement, about a quarter ton of carbon is sequestered, and the storage is effectively permanent. As is frequently the case with new construction products during early adoption, this cement is more expensive than the standard it is trying to replace.
Another process that will be needed to get the industry to zero-carbon will be the capture and storage of carbon from a plant’s gas emissions. This is happening on a small scale in some northern European countries. There are plans in the works to build the largest carbon-capture cement facility in the world in India with capacity to sequester half a million tons of CO2 per year.
Another measure to help the industry clean up is using advanced computer models to specify more exact quantities. Being a cheap form of reinforcement has led to more concrete use than needed, leading to significant waste. Additionally, designing structures for greater adaptive use will increase their longevity. If we use buildings longer, fewer new ones will need to be built, saving on cement. According to a 2018 European Union report, adopting these measures to use cement more shrewdly would shave a third off the building sector’s carbon footprint by 2050.